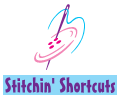
Hello all of you Happy Stitcher's!
Wow, can you believe it? This is the 5th edition of this blog! It is hard for me to imagine that I have written 5 already! It sure doesn't seem like it at all. I guess that must mean I enjoy what I do and sharing this wonderful craft with everyone! This will be part 1 of a series about thread. I say part 1 because when I first started to do research for this post, I thought to myself, "How much can I say about thread"? As I was getting into it, I realized that there is more to thread than meets the "eye"! (yeah, well, we have to get our laughs where we can!)
I know it is probably not high on your priority list of things to read, but it should be! With what we do it is one of the most important items of our wonderful craft, whether Sewing, Quilting, or Embroidery. I realize that right now you are thinking what is so exciting about thread, am I correct? Without it, we would not be able to enjoy many of the things that we do today, such as clothing, furniture, bed linens, and so on. The list is huge!
I can sometime imagine what the Eskimos must have had to do just to sew one simple garment to wear. They first had to either grind sections of fish bones into a very simple needle, called an "Awl", to use to attach their garments together. It was usually 2 to 6 inches in length. Or sometimes they may use a sharpened splinter of hardwood or a polished piece of ivory. Needles were prized possessions, with a hole chipped into one end and were as fine as the ones we use today.Using the large tendons of a deer, elk, or moose, then drying it. Once dried, they would either chew it or pound it to get it soft enough to use, then shred it. This was called "Sinew". The most common stitch used then was the running stitch. It is hard to imagine that today as now we simply go to the local fabric shop and choose from many varieties of needles. I imagine it was likely about the same for the American Indians also.
I have had a lot of people ask me how they can ensure they are getting a good spool of thread. The best way to tell is pull some off the spool, then hold it up to the light. Really look at it, if it appears to be what I call " thick and thin" then it is not a good spool. If it appears to look frayed in any way, I would go to another spool. Just because it is a name brand thread, does not mean that every spool that comes off the assembly line is a good spool. When you get a spool like this chances are it will be constantly breaking or fraying during use. Here are some microscopic photo's of some common embroidery threads.
Isacord
Mettler Metrosene
Sulky Rayon
Photo's courtesy of about.com
Madeira Metallic
It is easy once you really look at the different types of thread the differences between them. A good buy on thread sometimes is always not a "good buy". I have a whole box of thread I purchased on the INTERNET very cheap. Needless to say that is exactly what I received, a box of cheap thread! You get what you pay for and in this case I should have run away from the site! If the price is too good to be true, that is likely what it is, not true! This stuff was so bad that I actually pull it off the spools, cut it up and let the neighborhood birds use for nest construction, along with the hair I chop off hubby's head! That is really all it is good for. At least the neighborhood is colorful! So if you go to the fabric store and see some spools of thread with a few inches of thread pulled off, you will know why.
As far as how long a spool of thread is good for? Until you use it up! For me that usually isn't long enough to worry about it going bad! I have had some of it for quite a while, maybe 4 or more years (Thread Sale!), they are colors that you wouldn't use that often. However, thread can rot over a long period of time and when exposed to direct sunlight. I like to keep mine covered with some old towels I have for that reason. It also helps in keeping any dust off of it as well. Dust Can build up on it and cause problems for not only your sewing machine but it can cause it to break a lot also, at least until the dusty part is used up. Sometimes if I have left it out in the open for a period of time, I will pull off several inches of the thread and get rid of it.
The best I have used is Madeira(of course, I wish I could afford more of it),Sulky,Isafil, Isacord, Robison Anton, and Janome. Sometimes if I am looking for a specific color that I cannot find in the brands I like I will use Mettler, or Gutterman.Of course you all know that thread also comes in many different weights,as does bobbin thread as well.Ranging from 30,40,50,60 and many more different weights. A lot of the weight measurement depends on the manufacturer. They all seem to have their own weight system as well as their own color system.
Then of course you have the option of Rayon, Poly, Metallic,Cotton, Monofiliment, Neon, Silk, Solar Active, Glow In The Dark, Shrinking Thread, Variegated, Hologram, and Maxi Lock for sergers. This doesn't include all that is out there. Cotton thread is generally used for quilting. I have used monofiliment, but really don't like it that much. Each has it's own Characteristics for use. We haven't even gotten into the bobbin threads yet, which they also have different weights and grades like sewing threads.I have a certain bobbin thread I like and works very well in my particular machine, as I am sure most of you have found also. The one I use comes in three colors, black, tan, and white. This is another case where I strongly recommend that you go to your manual and see what the manufacturer says to use. Sometimes if I have issues with thread it is usually related to the type of thread being used.
Now we get into the Metallic threads, of which there are many different brands. The best way I have used metallic is by placing it in a coffee cup behind my machine, then running it over the top of my Thread Pilot, so it has a chance to relax a bit while using it. I also lower the speed of my machine to the slowest I have. (around 400) It is one of the most difficult to use for many folks. Patience is the key when using metallic thread! This for me has by far been the best method. Everyone generally comes up with a method that works for them and their brand of machine,I say stick with what you know works for you and your equipment! I always prefer to pay the extra money to buy a good Metallic thread as well. It is worth the extra money you pay for it, for ease of use and less breakage. I have used the less expensive brands, without much sauces. I will also pay the extra money for a good poly or rayon either one. It just makes sense to use the ones that give you the best results, with the least amount of breakage. It is also the best way I know of to guarantee success and a professional looking item.
I will say though, for you to stop and think about how many different places that the thread passes through before it gets to your needle. Back in the old days, you could actually see these parts and your tension disks. Now they are housed inside a covering to protect them from dust and dirt collecting on them. The down side to this is that you cannot see what is happening either. If you are not buying a good quality thread you may even be causing damage to the tension disks, eventually causing it not to maintain the proper tension. Are you really willing to risk the investment you have involved in your machine to save a few bucks on cheap thread? It can be an extremely costly repair bill, or worse yet, have to buy a new machine.
The next issue will go into more detail of the different types of threads and their uses,and there are many! I have just "scratched" the surface of it.
At this point I could go on and on, but I see you are starting to doze off on me so, instead I would like to introduce you to another one of our Central Florida ladies.
Meet Kathlene Bradford! She has recently had an article published in the SAGA (Smocking Arts Guild Of America) magazine's recent issue. If you click on her name it will take you to the media section where you can see a photo of her and what she does. If you go here, you can read the article about her, and the charity that is near and dear to her heart! It will not only bring a tear to your eyes, but will introduce you to someone who knows the meaning of giving, and how to get it done! Congratulations Kath, I am so proud to call you "Friend".
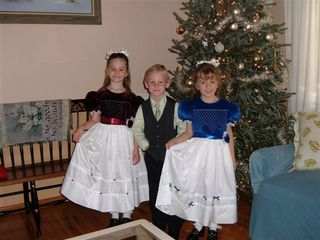
That's it for me, so until next time>>>>>>>>>>>> Happy Stitchin!
Judy
Remember to Kiss someone you love today!
Suzy's Tip Of The Week: When sewing slippery fabrics, pinning it is still the best method to hold it in place. it does take a lot of time but it is still faster than tearing out the seams and starting over. another method I have used and works quite well, is use a fusible tape along the seam allowance, then basting it. I really prefer the pinning method, i know it is the old fashioned approach, but that is what I have had the best luck with.
Fuse:>>>>> To fuse; means to glue two layers of fabric together, usually with an iron
Interfacing:>>> Is a non visible addition to fabric that adds body to an item, that the fabric alone doesn't have.
Appliqué':>>>> Is attaching a small piece of fabric to a larger piece of fabric to form a specific design or art.