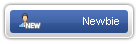 Rank: Newbie
|
Ok, so I've used my machine exactly 4 times and I am already having some major technical difficulty!! First I had the upper thread get all "globbed up" under the fabric and in the bobbin case. Removed all of that, all of the stray pieces I could see, etc. Worked fine for a little while and then started getting the "safety feature activated" or whatever message on my screen. When I push the start button, the needle moves briefly, vibrates about 5 times, then beeps and the message comes up. Does anyone know what might be causing this? I'm hoping that it might be something really simple that I might could try myself without making a trip to the shop already for repairs. SOOOO totally frustrating to be in the middle of the project and this happens!!!!! Thanks!!!!!!
|
|
|
|
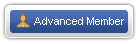 Rank: Advanced Member Was thanked: 1 time(s) in 1 post(s)
|
It sounds like you have thread jammed in the bobbin area.
Turn off the machine.
Remove the needle, foot and throat plate.
Remove the bobbin and bobbin case.
Clean out the the bobbin case, race and surrounding area.
When you put the bobbin case back into the machine, make sure it is properly installed (refer to manual). Hand walk the needle to be sure.
You will need the clean this area often, but once familiar with the process you will not have to remove the needle and foot, but do turn off the power for your own safety.
|
|
|
|
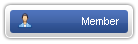 Rank: Member
|
Try pushing your presser foot "back" towards the back of the machine,gently! Sometimes, when positioning design in the hoop, the presser foot is not up and it will hit the back of the hoop and this will cause it to not be positioned correctly for the needle to sew "through the circle" of the foot. This will cause the needle to want to hit the frame of the foot, and the machine will send the safety feature message, which will stop the machine AND the needle from hitting the foot and breaking.
|
|
|
|
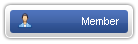 Rank: Member
|
Make sure that you are using the correct bobbin. I have the same problem when I have the wrong size of bobbin and there are a couple of them that look alike.
If the thread is wrapped around the bobbin, the bobbin is too tall.
Sue
|
|
|
|
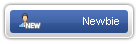 Rank: Newbie
|
My machine just started doing this today, "needle moves briefly, vibrates about 5 times, then beeps and the message comes up". Did you ever find out what was causing it?
|
|
|
|
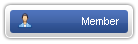 Rank: Member
|
If this started happening to me, I would take it in to the dealer. I would check the bobbin area, etc. but if after doing those things it still happened then I would definitley take it to the dealer. I know no one likes to do that but in some cases it is the best solution. I hope your machine is in good working order very soon. Thank you, kt3234 Karen
|
|
|
|
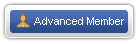 Rank: Advanced Member Was thanked: 1 time(s) in 1 post(s)
|
It sounds like a thread jam in the bobbin case area. Turn off the machine for your safety. Remove the needle, foot, throat plate and remove the bobbin and bobbin case.
Clean away thread snips and lint - this is routine maintenance.
If thread has wound around the mechanics, snip and remove with tweezers...gently. Do not tug on the thread. Moving the handwheel may help release the jam.
|
|
|
|
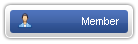 Rank: Member
|
Hi there; would like to know if you were able to get your problem solved, and if so, what was wrong.
|
|
|
|
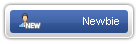 Rank: Newbie
|
I opened everything I could on the machine, I found no thread tangles etc, but I cleaned and cleaned and cleaned it anyway. Making sure I left nothing with even a speck of dust. Put the machine back together. And to my amazement it worked! But....... it stitched about 3,000 stitches and it did what it was doing before. There is no bobbin mess, nothing. It's like the needle freezes up. The hand wheel will turn only a 1/4 to the left and a 1/4 to the right.
I have taken my beloved embroidery machine to the embroidery machine doctor, but unfortunately they will have the machine for five very long weeks. UGH! Withdrawals. LOL
I will let you all know exactly what it was when I get it back.
Thanks for all your replies!
|
|
|
|
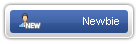 Rank: Newbie
|
Dear Sewing Friend
Would you please contact me privately so that we at Brother International can be of assistance?
Regards,
June Mellinger
june.mellinger@brother.com
|
|
|
|
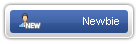 Rank: Newbie
|
I have been having the EXACT same problem. I am so very frustrated. I have had my machine for 6 months now. It has done it off and on. I have always had to take the plate off and take the bobbin casing out, etc. I did find that the needle had cut a bur in the bobbin casing. I filed it down and it began working again. But then it would always eventually happen again. I could usually keep on and on and finese it out of its fit. But a few days ago it began to do it constantly.
I took it to my authorized Brother repair man. He replaced the bobbin casing and said it sewed beautifully for him. I was so happy and brought it home. The VERY FIRST STITCH for me it did the exact same safety lockdown again! I called basically in tears and he said to bring it back in again. I dropped it off this morning and was called and told it was ready to go. When I picked it up this afternoon, AGAIN they showed what they stitched out and said that it had never caused a single problem for them.
I was skeptical but happy and came home to try it out again. It immediately started happening to me AGAIN! I forgot to mention that this is my 2nd Brother embroidery only machine and I have been embroidering for over 6 years with no problems until this machine. My other machine was a PE-150. I feel like I am going crazy! How can it stitch perfectly for him and do NOTHING for me??
Thank goodness, I have had one friend over watching me embroider something for her and saw how it was fine for most of her item and then went into the lockdown mode, OR else I might think I need to have my head examined. Needless to say, I now have a (in my opinion) expensive machine that will not work AT ALL for me and the repair man said he can no longer help me with this problem at all. He said I would just need to mail my machine to a Brother repair facility.
I am using the correct bobbin, I am using Brother brand bobbin thread, I have used numerous different top threads, I have reduced the top tension, I have used many different items and stabilizers, ALL with the same results - LOCKDOWN!
I am ready to throw this machine in a dumpster and cry! I truly LOVE to embroider things and am beyond sad about this whole situation :(.
|
|
|
|
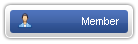 Rank: Member
|
I just received your reply this am - I understand your frustration. It might sound a little far-fetched, but have you checked your receptacle? (and did you plug your machine in the same one when you brought it home from the repair shop? Three thousand stitches aren't a lot - so something is happening almost immediately; just long enough to really get into a design.
I am grateful for this forum, but sometimes answers are hard to come by; I have been trying since last September to get better looking fonts when I made them small enough to do logo for a left side on a shirt or did them in an arch, which works very nicely for logos to add some interest without a lot of expense. It did help "some" to change the type of thread, but I didn't realize I NEEDED to do this; the Brother manual does not say that one NEEDS to following certain steps in order for designs to be what they should be. I don't generally skip steps, but I thought it was just saving information for the user's benefit.
The reason I am saying this is: call Brother International and ask them what they think this might be; they have been helpful over the phone, but the manual is vague when it comes to trying to solve problems, and you have a very unique situation. Just Google "Brother International"; perhaps you have already set up your account with them.
Keep us posted; once you find out, it will serve all of us.
Maddierae
|
|
|
|
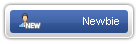 Rank: Newbie
|
Hi,
Thanks for trying to help out. I just got off the phone with Brother International. He asked questions and then felt that it is the little spring that keeps the bobbin casing from turning. He offered no other help though than that I can go to another center over an hour away or mail it to them in TN.
I know I was told that my local dealer could no longer help me with this problem but I think I am going to go there again today. I need for him to "see" what it is doing to me since he can't seem to make it mess up for him. I just hope he will be kind and work with me.
Beth
|
|
|
|
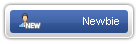 Rank: Newbie
|
Hi All,
I am OVER JOYED to report that I took my machine back to the Brother repair man again today. I told him what the Brother rep had said he thought it was. He said he really didn't think so but adjusted it anyway. Then I asked if I could sit and stitch something out so he could see what it was doing to me and he said sure. That is when I found out.....that it was ALL user error!
My old PE-150 was tough and rugged and would stitch anything with any thread, any stabilizer, etc. This machine is NOT so tough. It is finicky and particular! Once I used their stabilizer all of the problems seemed to be over. Well I have only stitched out two words but was just amazed.
I am now a total believer in having the right stabilizer, hooped the correct way, using the correct thread, correct bobbin, correct needle, etc. For any and all of you that are having this same message, once you have made sure that there isn't a lint build up in the bobbin area, go visit your local Brother store and let them teach you the correct way to embroider on this machine.
Beth
|
|
|
|
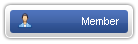 Rank: Member
|
Glad you got your problem solved!
When you say you used "their" stabilizer, what kind are you referring to? The majority of mine is from Madeira and AllStitch. I have noticed that is always the first thing is suggested when there is a problem, but Solvy and Madeira are considered as good stabilizers by all that I have read and been advised to use.
Maddierae
|
|
|
|
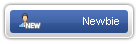 Rank: Newbie
|
I am not sure of the brand because they are sold by the sheet with no markings of any kind. They have very thick cut away that they double up and very thick tear away, again that they double over. It is 40 cents a sheet. I told the m that I was using Sulky and they were not a fan of it at all. While I was there a lady who runs a commercial embroidery business was in there buying it and also told me that it was the best and made all the difference in the world and she wouldn't use anything else. I asked her about the iron on/tear away and she said she always and only will use the ones I was buying and often uses the clear watersoluable stuff on the top too (can't remember the name right this second).
|
|
|
|
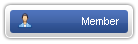 Rank: Member
|
[quote user="bethbest"]
Hi All,
I am OVER JOYED to report that I took my machine back to the Brother repair man again today. I told him what the Brother rep had said he thought it was. He said he really didn't think so but adjusted it anyway. Then I asked if I could sit and stitch something out so he could see what it was doing to me and he said sure. That is when I found out.....that it was ALL user error!
My old PE-150 was tough and rugged and would stitch anything with any thread, any stabilizer, etc. This machine is NOT so tough. It is finicky and particular! Once I used their stabilizer all of the problems seemed to be over. Well I have only stitched out two words but was just amazed.
I am now a total believer in having the right stabilizer, hooped the correct way, using the correct thread, correct bobbin, correct needle, etc. For any and all of you that are having this same message, once you have made sure that there isn't a lint build up in the bobbin area, go visit your local Brother store and let them teach you the correct way to embroider on this machine.
Beth
Beth,
I am so happy that your machine is in good working order once again! My machine is sensitive to the thread I use so I know a little of what you experienced. Thank you for sharing your situation and happy embroidering to you!
kt3234 Karen
|
|
|
|
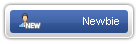 Rank: Newbie
|
Hi,
Well, lots has happened since my last post. I posted that it was fixed and I was so excited and in reality when I tried to sew here at home again - it was still broken. With no offer to help at all from my local repair man, I contacted the next closest place just over an hour away. They were so kind to me on the phone and told me they felt sure that they could help me. I took it there today and for the first time in 6 weeks, my machine is fixed!!! :)!! Creative Sewing Machine Center in Columbia, SC is my hero! Everyone in the shop reached out to me today. I can't say enough about them. If you live anywhere near Columbia, SC, you must go there!! I am going to mention all that was wrong with my machine in hopes that it can help anyone else having this problem, diagnose it.
It had a bur on the bobbin casing (yes the brand new one). It had a bur on the foot that after being filed down still caused problems and had to be replaced. The internal tension was off. But what I think was the #1 problem was that in the top where you thread the top thread, as you come down the last part, there is a tiny plastic bulge that the thread should go under and engage in the take up arm. Mine had a deep slit in it that was catching the thread and keeping it from going down and engaging. This was causing the top thread to be snatched into the bobbin area and break the top thread. Once filed down, it is working great again.
Boy, this has been a roller coaster ride to get it fixed properly but I feel I have reached the end. Brother International reached out to me and made me know that they were committed to seeing that it was repaired for me. I'm so happy I bought a Brother!
|
|
|
|
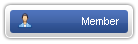 Rank: Member
|
You were very fortunate to find people that would take the time to help you and by you mentioning them, they have received great PR!!!
Thanks for letting everyone know what was wrong; that is quite a list and they need to be commended for taking the time to make sure they found all the problems - I just wish SC was closer to Northern Indiana!
Congrats and have fun finishing all you start from here on :)!
|
|
|
|
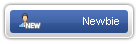 Rank: Newbie
|
my dealer told me to never use singer needles because they are to long and will score your bobbin cas and eventually cause you problems.
|
|
|
|
Users browsing this topic |
Guest
|
Forum Jump
You cannot post new topics in this forum.
You cannot reply to topics in this forum.
You cannot delete your posts in this forum.
You cannot edit your posts in this forum.
You cannot create polls in this forum.
You cannot vote in polls in this forum.
|